Idea Compass #5: Predictions
Carbon dioxide removal, decarbonizing transportation, and alternative proteins
So far, I've criticized ideas with the benefit of hindsight. I’ll admit that it’s easy to find flaws in ideas when history has told you where to look! It’s also much easier to be a pessimist than an optimist given that the base rate of failure for startups is about 90%. Pessimists get to say “I told you so” and look smart 90% of the time.
My goal is not to be a pessimist – the world has plenty of them already. Quite the opposite, I’m very optimistic about the role of technology in solving important problems like climate change, food security, factory farming, disease, etc.
As I argued at the beginning of this series, unprecedented leverage (digital, physical, intellectual, capital) raises the stakes of all ideas, good and bad. That’s why it’s worth red-teaming ideas more before putting resources behind them. When industries sink billions of $ or millions of person-hours into predictably bad ideas, it cools investment and slows down other solutions that are actually very promising. This certainly seems to have been the case for climate-tech.
To conclude the series, I'll stop looking backwards and instead make two sets of forward predictions:
Ideas and companies that I believe will turn out to be loonshots
Alternatives ideas that I’m optimistic about
I. Carbon Dioxide Removal
Loonshot: Macroalgae
One carbon dioxide removal (CDR) strategy that has been pursued by a few companies is kelp. Startups like Running Tide or Phykos are trying to grow gigatons of seaweed in the open ocean and sink it, where the carbon will be stored permanently (100+ years). I don’t think the math checks out.
Let’s start with the assumption that an offshore kelp farm could match the productivity of nearshore farms. This assumption is extremely optimistic, since nutrient levels in the open ocean can be much lower than nearshore. Nutrient limitations are why projects like ARPA-E MARINER have put so much funding/research into artificial upwelling systems that bring more nutrients to the surface. Indeed, Running Tide apparently struggled to grow kelp at all in the open ocean. A friend who worked there told me that they were sinking other biomass sources like wood chips to deliver on carbon credit orders.
Let’s do some math based on nearshore yields. Based on this report, average kelp farms in China yield about 20 tons dry weight per hectare (0.8 MMT annual production spread over 40k hectares). Assuming a 30% carbon content, this implies ~6 metric tonnes of C per year, or 6*3.67 = ~22 tonnes of CO2 removal per year. At $100/ton of carbon removal, the revenue for kelp sinking is then $2,200/hectare. Let’s say the system lasts 10 years. Then you have a budget of at most ~$22k to build a football-pitch-size (100m x 100m) structure that can survive in the open ocean for 10 years while autonomously growing, harvesting, and sinking kelp with no maintenance. It’s a tall order, and we haven’t even factored in operating costs, financing costs, or profit.
Let’s put the CAPEX in perspective. I used Greenwave’s kelp farm planning tool to design a 10 hectare farm1 that could achieve about ~11 tons DW/ha (only half of the 20 tons DW/ha target). This farm had a CAPEX of about $950k, or ~$95k/hectare. This doesn’t include buying a boat! If we get rid of anchors (the largest line item), the cost goes down to about ~$36k/hectare. This is the cost of low-tech stuff like ropes, buoys, and fasteners, which are already mass produced and unlikely to come way down in cost.
This 2020 techno-economic analysis from Green et al. found a production cost of $210-565/DMT (dry metric tonne). This 2022 paper from Kite-Powell et al. found costs in the $200-300/DMT range. The ARPA-E MARINER program has set its biomass cost targets at $80/DMT (~$72/ton CDR), since this is what they believe it will take to make cost-competitive biofuels.
Lo and behold, some Phase-II award hopefuls have produced TEAs showing that ~$80/DMT is possible (see the tornado diagram in this report). I’ve been unable to find any details of their model, but it appears that ARPA-E is assuming 50 DMT/ha yields. This would be 2-10x better than most nearshore farms that benefit from fertilizer runoff, nutrient dense water, and frequent human maintenance.
If you’re interested, this CarbonPlan model gives some cost estimates for ocean CDR using kelp. At some of the example sites they consider, CDR costs range from $375-2000+. This is in the same ballpark as other nascent CDR technologies, but doesn’t have the same future upside as an approach like direct air capture, which will get cheaper as renewables do.
It’s also worth noting that the US has tried to grow kelp in the open ocean for biofuels since the 1970s, and basically all of their experimental farms fell apart, sank, or were destroyed by the ocean. So I expect an autonomous open-ocean farm with nutrient upwelling systems to be inherently more expensive and robust than one that is anchored near the shore.
I’ll end with some of the other problems I see:
Seaweed doesn’t want to sink. So you need to pull it down to a depth where the high pressure will overcome its buoyancy.
Seaweed requires region-specific farming practices. Every ocean site may need the system to be tweaked, and a different variety of seaweed to be used. Permitting will look different in each country’s EEZ. It’s hard to achieve gigatons of carbon removal through bespoke regional solutions.
How do you prevent disease and predation across thousands of square kilometers of monoculture seaweed farms?
Ecology and leakage. If you blanket parts of the ocean in kelp, you might be out-competing other autotrophs and potentially disrupting the entire food web there.
MRV. It’s hard to verify that the biomass sank and was permanently stored, though groups are working on this.
Update (Feb 2025): This Volts episode on enhanced rock weathering (ERW) touches on Frontier’s negative results from macroalgae CDR at ~56:00. I’d recommend the whole episode as I do believe “low-tech” carbon removal approaches (e.g spreading crushed basalt or olivine rocks) are most likely to scale. Macroalgae might seem low-tech at first, but actually requires feats of engineering to work at scale.
Breakthrough: Land-Efficient Agriculture
(Yes, I am seriously including this in the carbon removal section.)
Carbon removal is a surface area problem. Whether you’re using kelp, direct-air capture, mineral weathering, biomass, etc, you need a lot of land or ocean area. You’ll commonly hear that we need to reach ~10 gigatons of CO2 removal per year by 2050, which implies that we’ll need to dedicate substantial land to carbon removal.
Agricultural innovations are the key to freeing up land for carbon removal. Over the course of human history, we’ve converted half of Earth’s land into pastures and cropland, losing carbon stored in vegetation and soil.
The land currently occupied by agricultural could be a massive natural carbon sink. This is known as carbon opportunity cost; the carbon removal capability that is forgone by using land for something else.
~80% of that agricultural land is used for livestock farming, even though only 17% of calories come from animal products. Meat is such an inefficient use of land that I felt compelled to write this blog post. If we let some of the ~40 million of square kilometers occupied by livestock regrow their natural vegetation and trees, we’d remove a massive amount of carbon from the atmosphere.
This is the theory of change:
Make alternatives to animal products that are cheaper, tastier, and an order-of-magnitude less land-intensive
Free up agricultural land that is no longer needed
Unleash biology
Turn free sunlight into stored carbon
Shifting to plant-based diets by 2050 would free up ~75% of agricultural land, remove an estimated 358-743 (mean estimate 547) Gt CO2 as ecosystems regrow over a period of 25-30 years. If you do the math, this is about 12-25 Gt of CO2 per year on average, taking care of our carbon removal needs. This doesn’t even include the massive avoided emissions from phasing out livestock, which Eisen & Brown capture alongside removals in their climate models.
A skeptic would point out that changing people’s diets is hard, and we may never fully replace livestock. They might be right. But even a ~10% reduction in global livestock production would give us an annually-recurring gigaton of free carbon removal!
You might also point out that soil and vegetation are not permanent carbon removals. Unless you’re selling carbon credits, this is fine. Carbon is fungible, so as long as we expand the total pool of biological carbon, what happens on the margins doesn’t matter.
II. Decarbonizing Transportation
Loonshot: Remora and selective optimism
Remora is a startup that’s adding carbon capture to semi-trucks. The idea is that the trucks capture the CO2 from their exhaust, temporarily store it onboard, and offload it while they refuel. The captured CO2 can then be sold to end users like concrete producers, or turned back into diesel fuel, creating a circular economy of hydrocarbon fuels.
I would celebrate their vision becoming reality, but I’m skeptical for a few reasons. First and foremost, I think they fall victim to selective optimism:
The company is very confidently betting against improvements in battery cost, electrification, and charging. They’re assuming that we’ll never have electrified semi-trucks or freight trains, so the only option is carbon capture and biofuels.
They argue that the current electricity grid is majority fossil fuels, so electrification doesn’t make sense. This is shortsighted. If you look at the exponential growth in renewable capacity and decline in carbon intensity then it would be wise to start electrifying things now!
They’re also betting against companies like Terraform Industries et al., who are making synthetic fuels from air (without a complex and circular supply chain)2.
On top of all this, they believe that biofuels will somehow start working after decades of failure to reach price competitiveness.
To believe Remora’s vision is the correct one, you have to be pessimistic about progress on basically every other climate solution except theirs.
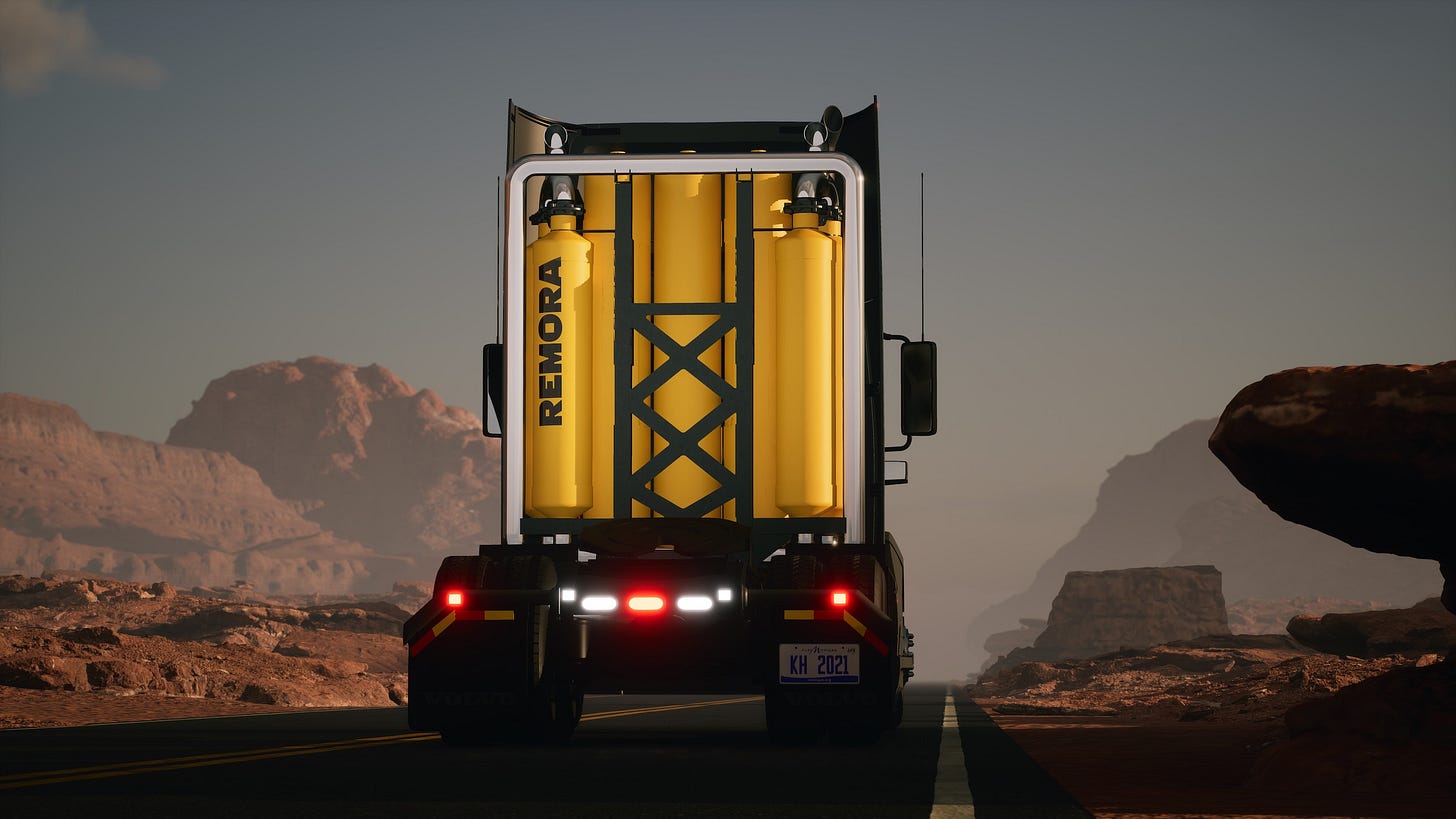
Second, the vision is internally incoherent. Remora imagines a world where we aren’t able to build enough renewables or batteries for electric vehicles, but we are able to build out a distributed network of CO2-to-fuel machines that can turn the captured CO2 back into diesel using… renewables3? If we have a great process for turning CO2 into diesel, why not just capture the CO2 from the air directly? Remora would argue that the captured CO2 from trucks is much more concentrated, making it easier and less energy intensive to synthesize diesel. But diesel isn’t just carbon atoms – there is a lot of hydrogen4 in there too, and that H has to come from somewhere. So Remora would need to produce green hydrogen, which requires… cheap renewables.
They also suggest that we’ll have abundant biodiesel (grown with crops), making their trucks carbon negative. Biofuels are a loonshot in their own right that have not become cost-competitive despite billions in government funding and decades of research. And if cheap biofuels did exist, then I’m not sure we’d even need Remora’s complicated retrofit system – transportation emissions would be largely solved already.
Breakthrough: Synthetic Hydrocarbons
Remora does make two arguments that I agree with.
We need to decarbonize existing transportation infrastructure, which means we need drop-in replacements for fossil fuels.
Second, the energy density of batteries is a real limitation. There are applications like long-haul trucking, shipping, and aviation where electrification might not work.
Carbon-neutral, synthetic hydrocarbons are the right direction. I’m a broken record at this point, but the theory of change for Terraform Industries is much more compelling: solar energy is getting so cheap that it will eventually make more economic sense to capture carbon from the air than dig it out of the ground.
For the details on Terraform’s approach, I’d recommend reading their whitepaper, and how they navigated the idea maze. The high-level idea is to do 2H2 + CO2 → CH4 using electrolysis (H2), direct air capture (CO2), and a Sabatier reactor (combining to form CH4). You could tweak the process to produce methanol or ethylene, which are building blocks for other industrially-relevant chemicals and materials.
There is no secret sauce – just three unit operations that each use dirt cheap commodity hardware and increasingly cheap solar energy. Other companies, like General Galactic, Rivan, and Turn2x appear to be pursuing a similar approach.
The advantages of this system are:
Whereas Remora is trying to capture carbon at millions of distributed point sources (tailpipes), Terraform can displace fossil fuels at the source.
By design, Terraform’s system gets cheaper as solar gets cheaper, which is a good bet to make. About 1/3 of their CAPEX is just solar panels5.
The system is simple enough to explain in a short whitepaper. They have three modules (H2, CO2, reactor) that can be mass produced in factories. Terraform controls and optimizes the manufacturing and deployment, and the only external integration is with natural gas pipelines.
No outsourced breakthroughs. There is no reliance on someone else to figure out a key piece of the vision (e.g, solving biofuels). Terraform’s only external bet is that solar panels get cheaper through the continuation of Wright’s Law.
That all sounds good, but can Terraform compete on cost?
In their most recent update:
March 2024: Terraform completes the end to end demo, successfully producing fossil carbon free pipeline grade natural gas from sunlight and air. We also achieved green hydrogen at <$2.50/kg-H2 and DAC CO2 at <$250/T-CO2, two incredible milestones.
In the chart below, this puts their prototype in the top-right corner (~$30/kcf). It’s worth noting that they earn a 45V green hydrogen subsidy that already gets them to price competitiveness, though this is a temporary tailwind.
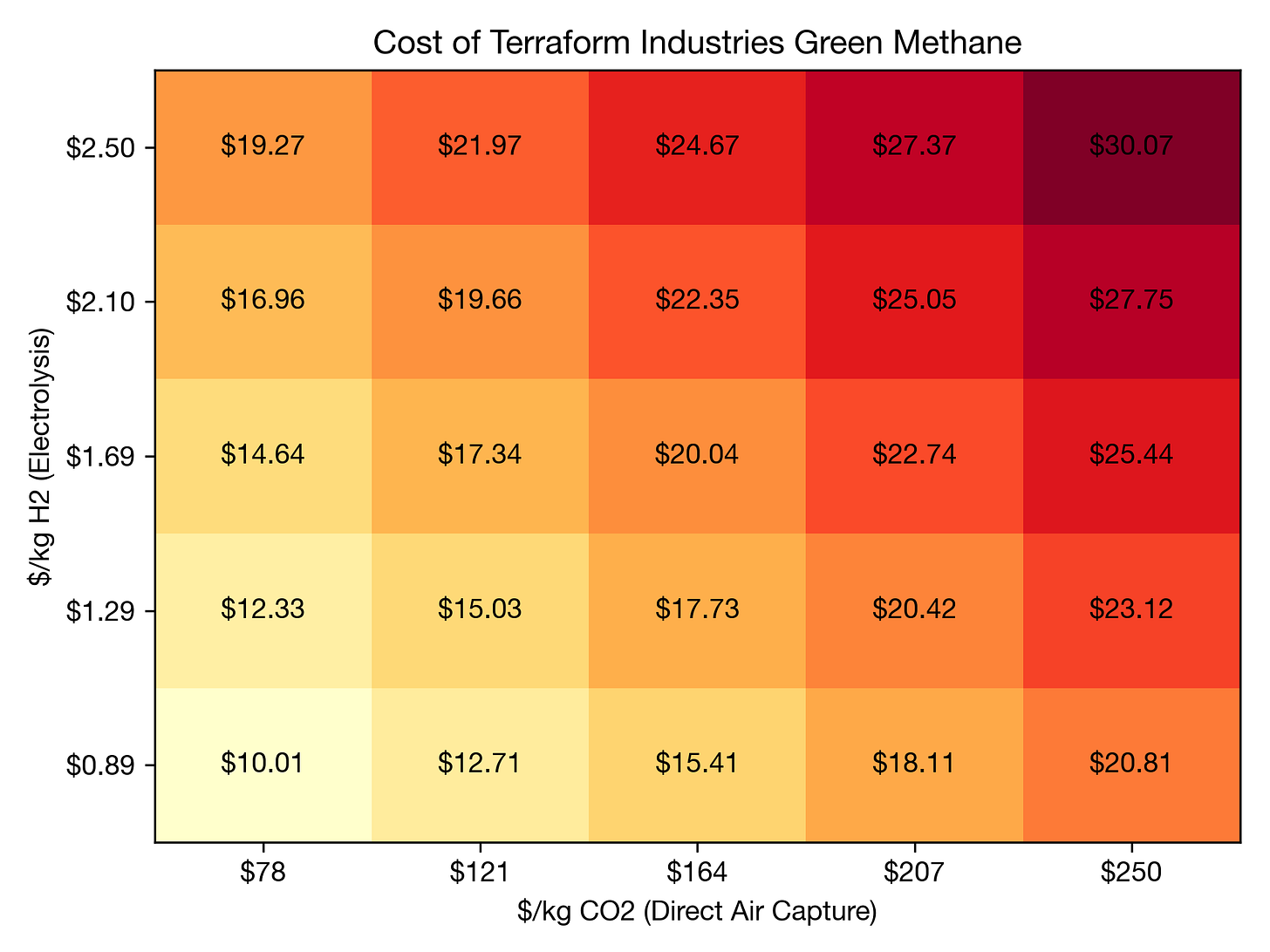
Terraform needs to reduce system cost by roughly ~3x to hit their long-term target of ~$10/kcf. This seems achievable for a hardware system moving from prototype to mass production in a factory, since Terraform’s modular system resembles something that could have an experience curve. Products that follow an experience/learning curve bring manufacturing costs down by a fixed percentage each time cumulative production doubles.
How quickly you believe Terraform could reduce costs depends on what reference class you choose, and how long you think the experience curve could last:
Solar: ~20.2% learning rate, ~50 years and still going
Lithium-ion batteries: 18.9% learning rate, ~35 years and still going
Gas turbine power plants: 15% learning rate, 1958-1990
If we think Terraform’s system looks like a gas power plant (15% learning rate), then it would take ~7 doublings of cumulative production to reduce cost by a factor of 3 (log base 0.85 of 1/3). If it looks more like a solar panel or lithium ion battery (20% learning rate), then it would take ~5 doublings.
Terraform is truly moonshot idea, and it’s quite possibly that they fail to raise enough money, make the system robust enough, scale up manufacturing, etc. Luckily, there are a few competitors in the synthetic fuels idea maze. I believe they’ve picked the right idea maze to be in.
III. Alternative Proteins
Loonshot: Cultivated Meat
Cultivated meat is a clear case of technological innovation with massive benefit to the world if successful. As I mentioned earlier, phasing out the livestock industry is one of the most impactful things we can do to address climate change.
I generally subscribe to the “price-taste-convenience” (PTC) theory of change, which posits that alternatives to meat need to be equal or superior along all three of these axes to gain adoption. By design, cultivated meat is on track to accomplish the “taste” objective. Cultivated meat is identical to the real thing, and could be precisely tuned to taste like the best steak or chicken breast you’ve ever had.
The problem of cultivated meat (CM) is the unit economics, which are analyzed in this extremely thorough techno-economic assessment from David Humbird. For a counterpoint on the Humbird paper, see this GFI post.
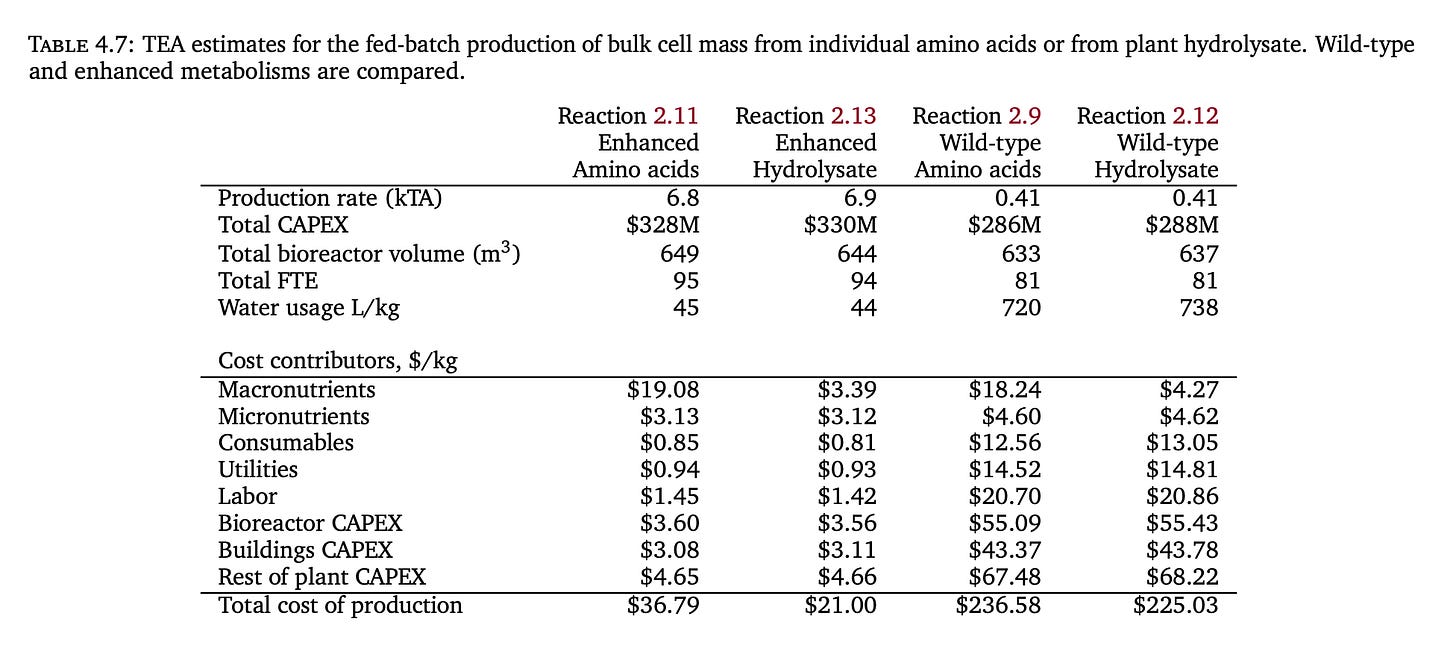
Let’s momentarily strip away all of the technological complexity of CM, and just think of it as a simple conversion of raw inputs to outputs. CM grows in a liquid medium containing macronutrients (amino acids and glucose) and micronutrients (electrolytes and growth factors). Pure amino acids are currently derived from fermentation, and prohibitively expensive. Even with significant economies of scale, about $19.08 of macronutrients and $3.13 of micronutrients are needed per 1 kg of meat (see table above). So we definitely can’t reach price parity with fermentation-derived amino acids.
If soy protein hydrolysates can be used as a cheap source of amino acids instead (not yet demonstrated commercially), the raw input cost is reduced to $3.39 (macro) + $3.13 (macro) = $6.52/kg (total raw inputs). But that’s around the total cost of boneless chicken breast! The raw input costs alone preclude price parity.
Now let’s layer on the CAPEX (~$11), labor, utilities, and other consumables, which brings us to an optimistic cost of $21/kg of cultivated meat. We’re still excluding the cost of turning a wet cell slurry into a finished product, packaging, marketing, transportation, and profit. We’ve also assumed a large number of technological breakthroughs, like scaffolding cells into a meat-like texture, achieving high cell densities, improving metabolic efficiency, remediating waste products, overcoming the need for cells to anchor to a substrate, precisely controlling stem cell differentiation, and so on.
Like Remora, cultivated meat requires selective optimism. It hypothesizes a world where the only viable way to displace meat is to grow genetically identical muscle tissue at massive scale and incredibly low cost. But if we can achieve this holy grail of biological and process engineering, why couldn’t we develop plant-based products that achieve taste parity?
Given sufficient knowledge, we can crack the magical recipe of amino acids, lipids, minerals, and water6 that make meat’s taste so hard to replace. The same goes for texture. If we can figure out how to make pluripotent stem cells grow on complex edible scaffolds, doesn’t it seem plausible that we could make big advances in structural protein design and plant-based processing techniques?
In my view, cultivated meat is an admirable but misguided effort, both a loonshot and a faster horse. People need food that is delicious, affordable, and convenient. Cultivated meat imposes unnecessary (and counterproductive) constraint that we must replicate animals exactly at the cellular level. This post, written by someone in the industry, summarizes why cultivated meat is so hard to pull off:
In reality, cultured meat requires unprecedented industrial processes to do almost everything that animals are so miraculously capable of. A few aspects of the living creature can be left out—including, notably, sentience—and others can be reused, but the challenge at hand is much more akin to creating and operating an artificial animal than to growing any one part in isolation.
Breakthrough: Hybrid Plant-Based Meats
Hybrid plant-based meats are mostly plants, with some cultivated or fermented ingredients added in to improve taste, texture, and/or nutrition. They could leverage the best of both worlds, combining the low cost and technological simplicity of plant ingredients with the unique functionality of fermented or cultivated ingredients.
It’s been a tough few years for plant-based meat, with sales basically flat or declining. I still think plant-based approaches have the best shot at winning the “price-taste-convenience” trifecta in the long-term.
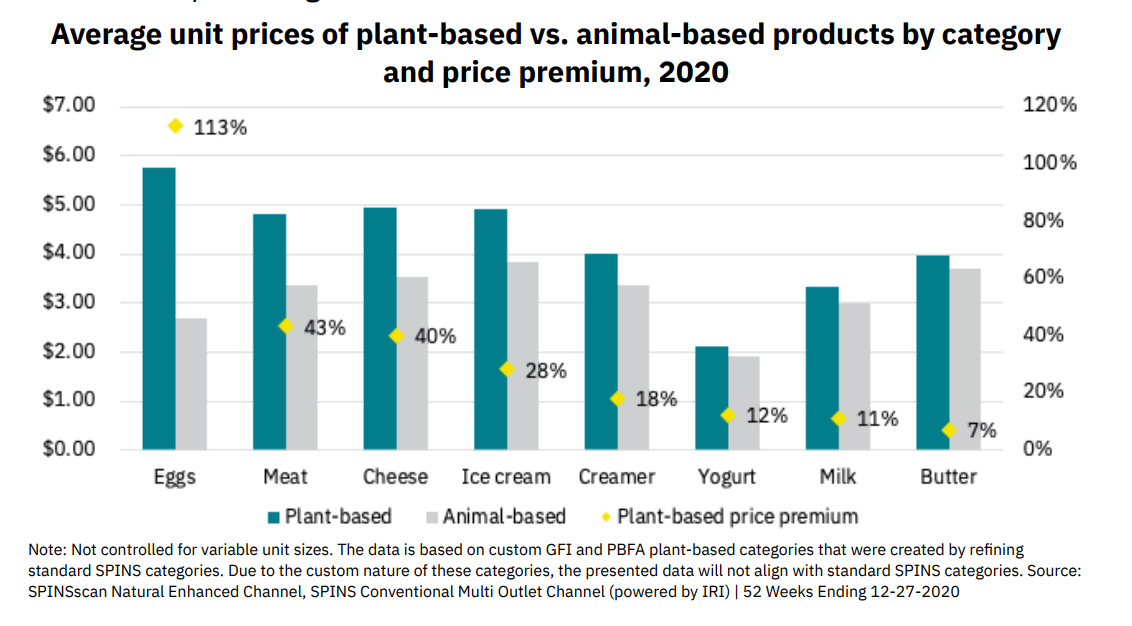
Price
Price is where plant-based products could really stand out. They’re currently more expensive than conventional options, but don’t have the formidable techno-economic hurdles of cultivated meat. By leveraging the cheapest raw ingredients, like soy or pea protein concentrates, so their unit economics are inherently more favorable.
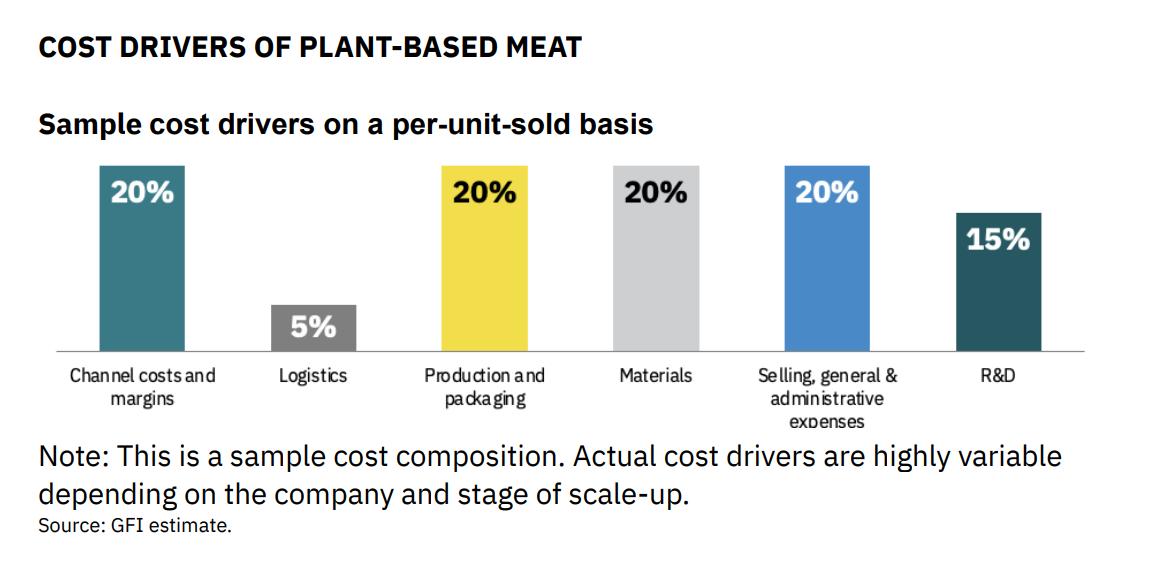
Above is an approximate breakdown of COGS for plant-based meats. I’m optimistic about cost reductions on all fronts except maybe “logistics”:
Channel costs margins are paid to manufacturers, distributors, and retailers just to get the product on a shelf. I imagine that the perceived risk of new plant-based products leads to somewhat higher costs in this category, and costs could come down a bit.
Production and packaging costs could come down with economies of scale, automation, optimized equipment, etc. Doing greenfield manufacturing instead of outsourcing to a CMO could be more cost-effective in the long-term.
Volume discounts from crop suppliers will bring material costs down, as would improved varieties of crops that are tailor-made for plant-based meat applications.
High fixed G&A and R&D costs are consequences of being a startup. These will be amortized significantly at larger scales. Claude tells me that mature food companies have R&D/G&A at 2-4% of revenue, compared to the 35% in the chart above.
For cultivated meat, the unit economics don’t actually look that much better at scale because the variable inputs costs (e.g macronutrients) are so expensive. For plant-based meats, the COGS are are very much driven by scale.
Taste and Texture
Taste is mostly a knowledge problem, not a unit economics problem.
Plants are extremely versatile, but have some key limitations. Protein concentrates from legumes (e.g soy or peas) might have some “off-flavors” that you need to mask. Most plant oils are liquid at room temperature (coconut and palm are exceptions) and melt differently than those in meat. It’s telling that 68% of plant-based producers would like to include cultured fats in their products! Last but not least, plant proteins may not have the same gelation, emulsion, or structural properties as meat tissue.
These seem like solvable problems. You could edit or breed crops to reduce unwanted flavors. You could add precisely tuned fats (via cultivation, fermentation, or a chemical process) at small inclusion rates that complement those in plants. You could design new fermented protein additives that interact with the plant proteins in interesting ways to change texture. Including one or two “magic ingredients” like cultivated fats and structural proteins could reduce the need for other additives, and actually shorten ingredient lists7. Lastly, there could be a lot of taste/texture gains from hardware innovation. If you’re in the Boston area, go try Tender Foods for an example this.
Convenience
Convenience is a consequence of scale and adoption, so it’s downstream of making a great product. If you make food that’s affordable and delicious and have a decent strategy for getting it into restaurants and grocery stores, convenience takes care of itself.
Conclusion
Plant-based products have a clear path from taste → price → convenience → adoption. It won’t be easy by any means, but taste and texture can be solved with more R&D, and price will come down as companies scale up.
With taste and price barriers out of the way, we’ll get a flywheel of consumer adoption leading to more availability leading to more adoption.
Whereas cultivated meat starts with taste parity, and tries to solve near-impossible unit economics, plant-based products start on a sound techno-economic foundation and work steadily towards taste parity. I’d bet my money on the latter approach.
If you've made it this far, thanks for reading! If I’ve gotten something wrong, I’d love to hear about it.
The Massachusetts farm is ~24 acres (10 hectares), uses a 5-line design, and yields 1.6M lbs wet weight per year (only half of the 20 tons DW / ha goal). I had to max out most assumptions to achieve this yield: 100 arrays spaced at 10 feet apart and 16 pounds of kelp per foot of line.
Remora is capturing carbon at the most difficult (wide/distributed) end of the funnel. There are thousands of oil and natural gas fields in the world, but billions of vehicles and other end-uses. To put a dent in vehicle emissions, Remora needs to retrofit millions of trucks around the world to include carbon capture and storage. Instead of adding point-source capture to millions of tailpipes, you could displace the same amount of emissions with orders of magnitude fewer factories producing carbon-free fuels.
And these renewables would almost certainly require storage (i.e batteries) to enable continuous 24/7 operation!
Diesel fuel includes a range of hydrocarbons, from C10H20 to C15H28, with an average molecule of C12H23. I did some back-of-the-napkin math here to see how much of the synthetic diesel cost comes from hydrogen vs. CO2. In a Remora-like scenario with $100/ton captured CO2 (cheap) and $2/kg H2, the cost breakdown is about 50/50. If CO2 costs $350/ton, then the breakdown is more like 80/20 CO2:H2. In either case, the cost of H2 matters, but it matters even more for Remora’s use-case.
Solar is currently at ~$0.3/W, and Terraform’s targets are based on a long term assumption that solar will hit ~$0.1/W. At $0.1/W, Terraform’s module will cost $30k, and need about ~$16k of solar installation (1/6th of a 1MW solar farm). This is where my 1/3 of cost from solar number comes from.
A number of companies are focusing on blended products, where the cultivated meat or fat is used to enhance plant-based products at low inclusion rates
I think the “long ingredient list” argument against plant-based foods is extremely dumb, and will turn out to be a psyop from incumbent meat and dairy companies. The number of ingredients is a poor proxy for healthiness; is a salad less healthy than each of its constituent ingredients? Meat and dairy companies can feed anything they want to livestock and sell the result as “1 ingredient” without disclosing the hormones, antibiotics, palm oil, etc on the label.